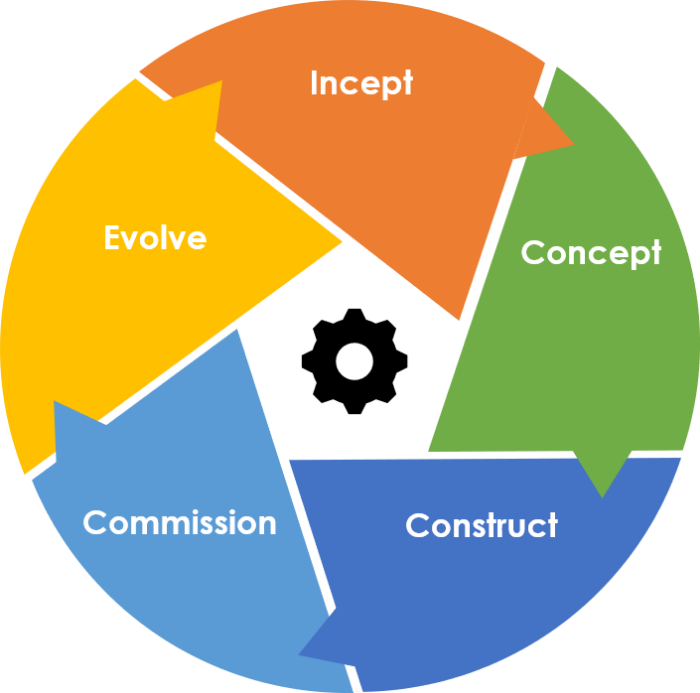
DISCIPLINED Methodology for
Project Delivery
Our professional team can deliver complete automation projects based on our in-house implementation methodology by blending common engineering practices in process industry with software development life cycle to present a unique delivery methodology. RMS methodology is characterized by:
01. Complete
RMS process begins before project start when customer is still in the inception phase. We help him to understand and build his roadmap then move to project initiation, then design and implementation, and even beyond production by ensuring system continuously run in healthy manner and analyze the performance to prepare for planning of the next improvement project.
02. Iterative
No Big Bang! Any automation project is built gradually through short iterations and demos can be executed for end customer in the middle of project execution to ensure no deviation from customer requirements unless project is quite simple and short.
03. Clear
Each phase has clear activities that need to be executed, roles that will execute these activities, and work products that will be delivered.
04. Adaptable
While Waterfall and Agile methodologies are on two different sides of software development methodology spectrum, time has proven that no one-size-fits-all. Our process tends to have big transitional phases like Waterfall and under each phase small iterations are executed, while, adopting some Agile practices that allow faster development and accommodation of small scope changes. However, we can change phases, iterations, work products within certain limits to adapt to project nature, size and project situation
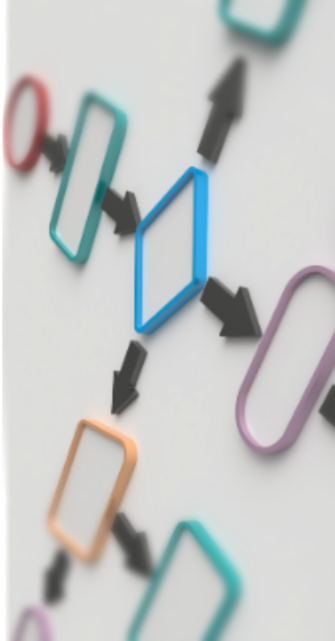
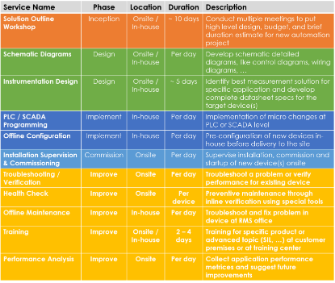
Services CATALOG for
Individual Services
We have developed set of services as prepackaged products with specific scope, average duration, and clear output. These services will fit with different phases, such as "Solution Outline Workshop" at Inception phase, "Instrumentation Design" at Design phase, "Training" or "Health Check" at Improve phase.
Still we offer what fits you
Despite having these predefined services, for sure RMS can offer customized services that fits customer requirements.
package services as
service bundles
RMS grouped certain services together to allow our customer have full control and active preventive maintenance for their automation and instrumentation solution.
TIERED BUNDLES
Based on customer plant size, number of instrumentation assets and control size, he can have "Startup", "Extended" or "Ultimate" service bundle with each has guaranteed service level agreement, number of free commissioning, troubleshooting, health checks visits, training courses, etc. depending on the chosen bundle.
CUSTOM BUNDLES
Still custom maintenance contracts and special service agreements can be developed fitting with plant conditions and customer requirements.
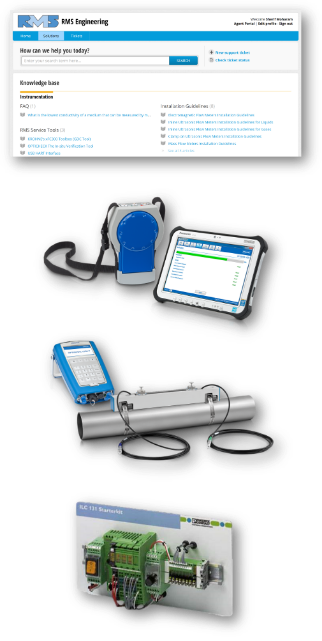
service tools for
outstanding service support
Our services team has acquired certain hardware tools, software systems and skills to give our customers outstanding support outperforming market norms.
SERVICE SUPPORT PORTAL
Online helpdesk that facilitate for customers reporting any problems or technical questions and manage their tickets. It also include knowledge base with several articles about installation best practices, troubleshooting and configuration tips.
VERIFICATION TOOLS
KROHNE OPTICHECK tool gives the capability to verify KROHNE electromagnetic, Coriolis mass, and vortex flow meters as well as the latest series of KROHNE radar level sensors. Verification is done inline without need to disassemble the device. This gives customer the relief of having to interrupt the process and calibrate the devices.
flow measurement as a service
With KROHNE OPTISONIC 6300 portable clamp-on ultrasonic flow meter, RMS can offer flow measurement as a service. This has significant cost saving for customer maintenance engineers when they need to temporarily measure the flow at specific point or want to verify performance of existing flow meter.
interface adaptors
Many interface adapters available for our partners devices or generic adapterts, such as HART USB adapter that can interface with any HART-enabled instrument regardless of the manufacturer.
spare parts & training kits
We have stock of flow meter converter, temperature transmitters, and pressure transmitters that allow us to respond quickly to plant emergency needs. In addition, we have Demo kit for Phoenix Contact inline controllers and several instrumentation devices to ensure a hands-on practical training is given to customers' engineers.
Now you can navigate through the in-stock products using our online eShop and book your products.